Wondering how much weight your pallet racks can safely hold? This chart on the pallet rack load capacity chart covers everything you need to know. The article includes key components, accurate calculations, and safety best practices to prevent accidents and streamline your warehouse operations.
Key Takeaways
- Understanding pallet rack load capacity is essential for ensuring safety, preventing accidents, and optimizing storage efficiency in warehouses.
- Key factors affecting load capacity include beam length, upright frame design, material quality, and the maximum unsupported span between beams.
- Regular maintenance and inspections of pallet racking systems are crucial for sustaining optimal performance and safety in warehouse operations.
The Importance of Understanding Pallet Rack Load Capacity

Understanding the load capacity of pallet racks is crucial for safety in the storage environment. Overloading can result in accidents, damaged goods, and severe injuries. Adhering to weight limits prevents these incidents and maintains structural integrity.
Warehouse staff must know the weight capacity of racking systems to avoid overloading and ensure safety. This information helps prevent accidents, streamline operations, and enhance productivity. Optimized load capacities allow efficient allocation of storage space, reducing inefficiencies and maximizing vertical and horizontal storage potential.
Ensuring safety ultimately lies with warehouse owners and managers. Accurate rack capacity calculations and adherence to weight limits fulfill their duty of care towards employees and goods. The mantra “better safe than sorry” underscores the need for vigilance and compliance in warehouse operations.
Key Components Affecting Pallet Rack Capacity
Several factors influence pallet rack capacity. Beam capacity, for example, defines how much weight a beam can support without excessive bending. Longer unsupported spans between beams can reduce overall load capacity due to increased deflection risks.
The upright frame design, including its shape and bracing, significantly impacts load-bearing capabilities. Each upright frame bears half the loads of each attached beam pair, making their design and material quality critical. Beam connectors, whether pins, hooks, or bolts, are vital for maintaining load capacity and stability.
Material quality, the distance between beam levels, and the overall design of the pallet rack system are additional critical factors. Adjustable pallet rack frames can change in capacity based on beam placement, affecting load stability. The type of material stored and pallet size also play significant roles in determining overall rack capacity. Together, these factors ensure the racking system can safely carry the intended loads.
How to Read a Pallet Rack Load Capacity Chart
Reading a pallet rack load capacity chart ensures the safe use of racking systems. Provided by manufacturers, these charts outline load capacity based on the steel grade and component thickness. Clearly posting the maximum load capacity prevents overloading and potential damage.
The deflection rate, or the amount a beam bends under load, is critical to consider. For standard conditions, the maximum allowable deflection rate for rack beams is 0.55%. In more demanding environments, such as those using robotic systems, a stricter deflection rate of 0.42% is recommended. Load capacity labels on each bay are the most common method for displaying weight load capacity information in the rack configuration.
Pallet rack decks are designed to evenly disperse pallet loads across beams, enhancing stability and capacity. Understanding how to read and interpret these charts ensures that warehouse operations remain safe and efficient.
Calculating Upright Frame Capacity
Calculating upright frame capacity is crucial for determining the overall load capacity of your pallet racking system. Key factors include frame height, leg dimensions, and construction materials like cold-formed steel. Upright frames must support both static loads from the rack and dynamic loads from moving pallets.
For example, a typical pair of 144” upright frames can sustain a total weight of 16,700 pounds, while a larger 192” frame can handle up to 25,300 pounds. As the space between beam levels increases, the overall load capacity supported by the frame decreases.
Accurate calculations ensure your racking system can safely support intended loads, preventing accidents and structural failures. Understanding capacity ratings and using capacity charts allows effective management of warehouse storage space while maintaining safety standards. Normally, racking manufacturers or suppliers will calculate it as to their products and let you know.
Determining Beam Capacity
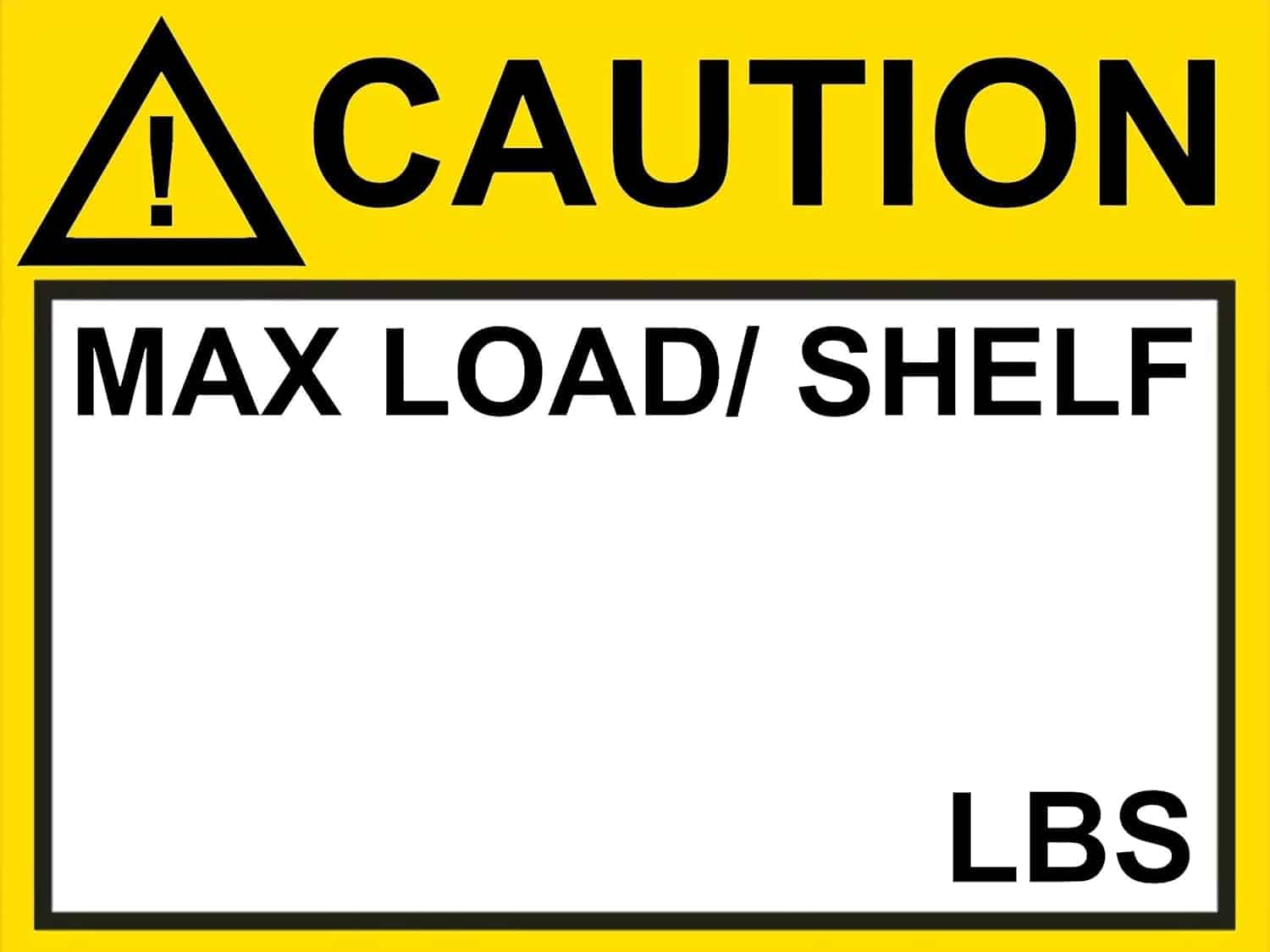
Determining beam capacity is essential for managing pallet rack load capacity. Factors such as beam length and vertical spacing critically impact overall capacity. Longer beams need to be deeper to support the same weight as shorter beams.
The heights, depths, and design of the frame affect the maximum load of pallet racking beams. To calculate the maximum load per pair of beams, consider the combined pallet racking weight of the pallets they support. For instance, a pair of 96” rack beams with a 3.5” depth can hold 4,044 pounds. Increasing the beam depth from 3.5” to 4.3” significantly increases the pallet racking weight capacity to 6,111 pounds.
Deflection, or the bowing of racks under loads, poses safety risks when beams are overloaded. Understanding beam deflection and using correct capacity ratings ensures the safety and stability of your pallet racking system.
Maximum Unsupported Span and Its Impact
The maximum unsupported span, or the largest opening between beam levels, determines the load-bearing capacity of the racking system. Increasing the distance between beam levels reduces the overall capacity the rack can safely support.
Uneven weight distribution across beams can lead to structural failure. To mitigate these risks, consider installing intermediate beams or reinforcing columns to reduce unsupported spans and redistribute the load. Managing the unsupported span enhances the stability and safety of your pallet racking system.
Using Load Capacity Charts for Different Configurations
Using load capacity charts correctly is crucial for different rack configurations. The configuration of a pallet rack system, including the number of uprights and beam spacing, significantly impacts its overall load capacity. Use the load capacity charts provided by the rack manufacturer, as they are based on specific design and material factors.
The arrangement of beam levels influences the maximum load per level; fewer levels allow for heavier items. Following the manufacturer’s guidelines and understanding capacity ratings helps optimize racking configurations for maximum efficiency and safety.
Maintaining Pallet Racking Systems for Optimal Performance
Maintaining pallet racking systems ensures safety and optimizes load capacities in warehouses. Regular inspections significantly enhance worker safety and minimize damage to goods. These inspections should identify and address issues like excessive unsupported spans, which can affect safety.
Pallet racking should be inspected upon installation and regularly thereafter to identify any damage. Regular maintenance and inspection of pallet rack beams are essential for long-term durability and safety. Using mobile technology for inspections can improve the efficiency and accuracy of these assessments.
Maintaining your pallet racking systems and ensuring they are in optimal condition creates a safer and more efficient warehouse environment.
Summary
In summary, understanding and managing pallet rack load capacity is vital for ensuring warehouse safety and efficiency. By knowing the components that affect rack capacity, reading capacity charts correctly, and maintaining your racking systems, you can prevent accidents and optimize storage space.
Remember, the key to a safe and productive warehouse lies in vigilance and adherence to load capacities. Keep your racks in top condition, and you will see the benefits in both safety and operational efficiency.
Frequently Asked Questions
Why is understanding pallet rack load capacity important?
Understanding pallet rack load capacity is crucial for ensuring safety and maintaining the structural integrity of the racking system. This knowledge helps prevent accidents and safeguards personnel and inventory.
What factors affect pallet rack capacity?
Pallet rack capacity is primarily influenced by beam capacity, frame design, material quality, and the spacing between beam levels. Understanding these factors is essential for ensuring safe and effective storage solutions.
How can I read a pallet rack load capacity chart?
To effectively read a pallet rack load capacity chart, focus on the steel grade and thickness specified, along with the deflection rates and load capacity labels. This will ensure you understand the maximum load each component can support safely.
What is the maximum unsupported span, and why is it important?
The maximum unsupported span is the largest distance between beam levels, which is vital for ensuring the rack’s load-bearing capacity and preventing structural failures. Proper management of unsupported spans is essential for maintaining safety and stability.
How often should pallet racking systems be inspected?
Pallet racking systems should be inspected regularly from the initial installation to identify and address potential issues, ensuring long-term safety and efficiency. Consistent inspections are crucial for maintaining safety standards.